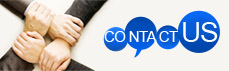
- Jiasheng New Material
- Cell phone:+86-13357880827
Contact:Mr Mao
TEL:+86-519-88400185
- E-mail:wangxiaoying@czjswfb.com
maozhiqiang@czjswfb.com
- Address:No.200,Ronghu Road, Hengshanqiao Town, Economic Development Zone, Changzhou City, Jiangsu Province
Nonwovens used in automobile
2015-04-03
China, woven in the automotive market plays an important role. Filter sets from the cockpit and the seat to the trunk lining, insulation blankets and carpets cloth. According to the current annual production of 700,000 cars per year demand for non-woven insulation blankets will reach about 2.45 million square meters. 2000-2005 China "Textile Industry and Technology Development Project Guide", and non-woven fabrics and industrial textiles industry-related projects have 15, including "car research and product development with interior materials." The study includes knit trim materials, flame retardant, antistatic car velvet woven decorative materials, structural interior fiber-based composites. Goal is to replace imported fabrics for interior decoration matching car, in line with luxury, comfort, safety requirements, the flame retardant and antistatic properties of the leading domestic level.
Non-woven fabric can be used for insulation, air filtration, insulation, enhance and improve occupant comfort and reliability. In addition to these advantages, from 40 years ago began to be used automotive parts. Nonwovens also because of the high strength and durability are many car companies recognized as economical material. With the application of non-woven fabric in cars is growing, competition to participate in this market between coil manufacturers also intensified research and development work in this area is also intensify.
In recent years, the German automobile company Sandler Affairs Schwarzenbach / Saal KlauTroeger sales manager said. Car manufacturer requirements facilitated the development of the special non-woven "These products continue to improve and enhance the new development of processes and materials for the industry to continue to break with the non-woven textiles are areas traditionally occupied by paving the way" consumer demands for vehicles with non-woven fabrics are mainly low-cost, highly efficient filtration and sound-absorbing materials.
Carmakers in research using these products to replace higher-cost materials such as leather seats. Usually not noticed by the driver or passenger, along with the introduction of the new car nonwovens. Non-woven hidden in the seat or carpet, or other fabric sewn together to improve the strength and durability. Mr. acupuncture fabric suppliers Amoco Fabrics and Fibers industrial fabrics Branch Manager EdwardMerchlinski believe that acupuncture is very suitable alternative to leather fabric for the seat, because he is more economical, and in Latin America, sticky, sewing process is easy to operate, suitable for sewing.
Non-woven fabric becomes more firmly
Automobile manufacturers are increasingly clear, environmentally friendly non-woven fabric characteristics that it can replace the foam product used in an automobile. According to the statement, Mr. DanKamat PrecisCustomCoat company vice president. Compared with other materials, non-woven fabric has the environmental advantages.
Caralsois widely used asan alternativerubberskeleton reinforcedrubber sheetmaterial,andrubbercompoundmade ofsteel ringjacket,car steeringconnecting ring,seal, andwitha modified rubbercompoundused in thefenderandtirematas well asthe floor.You canimprove the strength, abrasion resistance, flexibilitycomponents,in addition.Extended service life.
These materials in the engine hood lining, headliners, instrument panels and other small acoustic and thermal insulation in the interior parts used more and more. This can be bonded nonwoven from PCC acupuncture and heat business growth glimpse.
Nonwovens manufacturers therefore developed an alternative to foam and recycled materials can be used. In addition, it also with glass fibers and recycled materials are very strong together, automobile manufacturers can not hope to stop the use of recycled foam. When stretching, uniform color, no wrinkles and tear.
The new products have been developed for the stitching of automotive interior parts, Germany specializes in the production of automotive chemical bonding, mechanical consolidation and thermally bonded nonwoven fabric companies eswegeVliesstoff also felt nonwoven textiles substituted trend. Such as car roof or glove compartment. Other environmentally friendly stitched fabric is also being developed for the composite alternative for the seat foam.
Can be effectively used to replace more conventional flame-bonded nonwoven fabric - foam sandwich material, Eswege's composite nonwoven fabric is produced by hot melt lamination. And can be completely recycled. The company is located MittweidaTechtex stitch production line Multiknit and Kunit nonwovens, can replace up to 8mm foam drink.
Produce a gram weight of 200-2800 multiaxial nonwovens. Composites can be used glass fibers, carbon fibers and combinations of fibers and said fibers of aromatic.
And rapidly replacing traditional fabrics, nonwovens despite giving the car a lot of advantages. But carmakers and consumer demand ultimately determines the most popular car models and sizes. Naturally, the year the number of cars sold and manufacturer of non-woven varieties will have a significant impact. Mr. Amoco's Merchlinski that the car style, size and the use of material changes in the trend rate can be very fast, the time period can be measured in months.
Make participation in this market is fierce competition, if car manufacturers like bucket seats. This demand will rapidly spread in the automotive industry chain. Manufacturers also must be able to respond to this change at any time, providing the right products.
Makes it to invest more in product development, shorten the product development cycle for companies made new demands. And increased interaction with OEM manufacturers.
Kureha chosen as the ideal combination of a water-soluble synthetic resin and an adhesive material, in order to provide more efficient filter. The design of the bus with thermally bonded nonwoven fabric. Filters for engines such like. Such filter materials may be molded in accordance with the specific filter. Colbond cab is also provided for the filter is used as the thermally bonded nonwoven fabric ColbackColback cab filter support medium, and the molded automotive carpets and carpet backing material. Colback polyester used as a core, two-component polyamide filament nylon for the skin, with good thermal and mechanical stability, the polyamide layer of the cortex can be used in combination with various dyes and paints have a good affinity and capacity.
With high toughness, permeability and homogeneity. Costs are driving growth in the automotive market nonwovens major power, Colback main advantage is that it can be used as carpet and a preformed tuft bind and has good wear resistance. When used as a support medium inside the filter. But also become a major obstacle to nonwovens manufacturers, because in the past few years, the global economic downturn, OEM to first- and second-tier automotive suppliers exerted tremendous pressure, which affects the entire supply chain participants, including membrane production providers, because he is also struggling for expensive raw materials.
Noting automobile manufacturing market latecomers to show a tendency to say, Mr. Verbakel Colbond's sometimes excessive focus on the individual component costs has led to the total cost of the final product quality or neglect. I believe can be used to meet the needs of high-volume production lines, he napped surplus. This is bad for everyone, not just because of the high price pressure, as well as logistics and quality requirements. Original equipment production line stagnant price is thousands of dollars per minute, regardless of the manufacturer web Boli sales or car manufacturers at below-market prices to buy these materials, they can not compensate for these high risk.
That is to buy a car once thought to be needed after a long research process has now become an online anonymous quotes, gambling game Mr. Verbakel noticed another trend line auto auction.
Environmental factors
Nonwovens suppliers still trying to produce products that meet automotive recycling regulations will take effect in 2006 in Europe, the product, in addition to the price factor. Requires 1% of car can be recycled, recyclable and thus open the door to many opportunities for the non-woven fabric.
The main reason is due to the law of the imminent entry into force of Europe. But the global nonwovens manufacturers still assure customers, car recycling more attention in Europe than in the United States. North American products can be recycled for recovery are also interested, but not as good as it is not mandatory so important in Europe or demanding. Those involved in the automotive industry in Europe coil manufacturers are implementing a new quality management system to meet these requirements.
Global Molecular institutions have implemented the this system. As eswege to implement a new quality management system to meet quality standards and DINENISO14001VDA 6 DINENISO9001 and EU environmental requirements. In order to provide customers with the benefits of standardization.
But experts believe that this will be the trend in the next few years. Recyclability not only conducive to the car, although some non-woven production enterprises have not fully turned to the production of recyclable automotive products. Because of the high loft, no pure polyester non-woven adhesive demand will increase, while also providing a safer non-woven production process.
So that they can adapt to changes in the auto industry, whether it is auto manufacturers or nonwovens manufacturers are constantly adjusting. Both R & D activities did not show any signs of slowing down.
Car nonwoven fabric is probably the most notable soundproofing material. Sandler with the launch of sawasorbplu and sawaform products in the coming years. The former is made of pure polyester material, low weight, low combustion performance. Future products will be market-oriented and traditional R & D and customized combination of more complex non-woven fabric will be used to advance high-tech sector must recognize the future needs and requirements, and the blend fabric in versatile .
FFT into the trunk of a car in North America, said more than 40 percent of the market supply trunk trim panels, molding Fiber Technology Co., Ltd. (FFT major North American automotive OEM thermoforming, nonwoven system solutions providers and tier suppliers. Currently The company is also seeking to continue to expand market share in this market and other interior components.
FFT is MorgenthalPartner acquired in 2003. The latter is intended as a platform for an inferior race, the acquisition of other fiber solutions provider, constructed automotive and non-automotive markets leading one-stop supplier of fiber products and systems. FFT while the production of yarn dyed polyester fibers for the textile industry from 100% recycled materials for industrial and civil production.